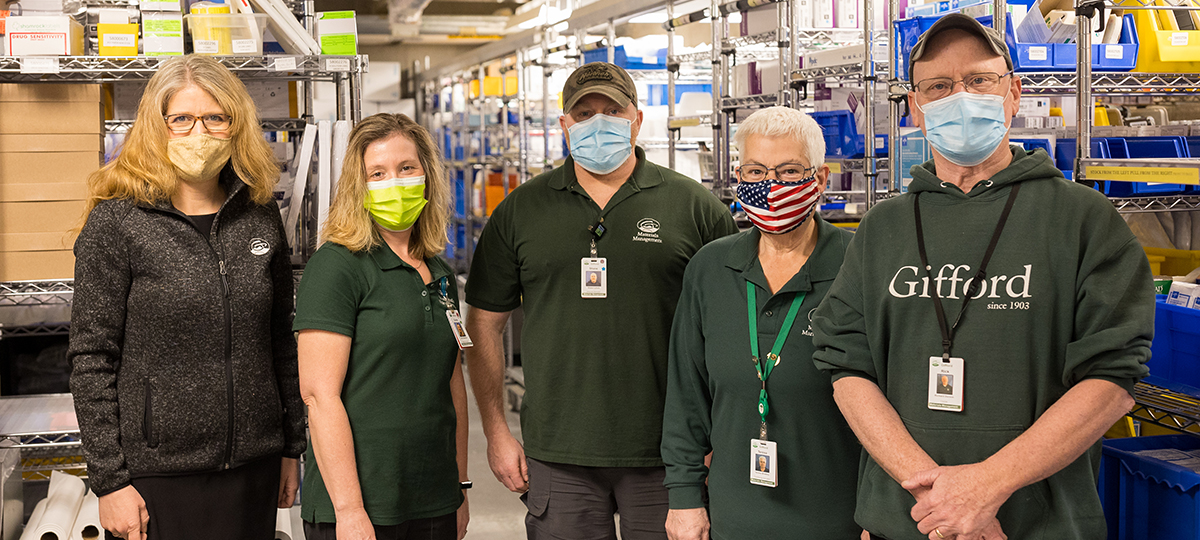
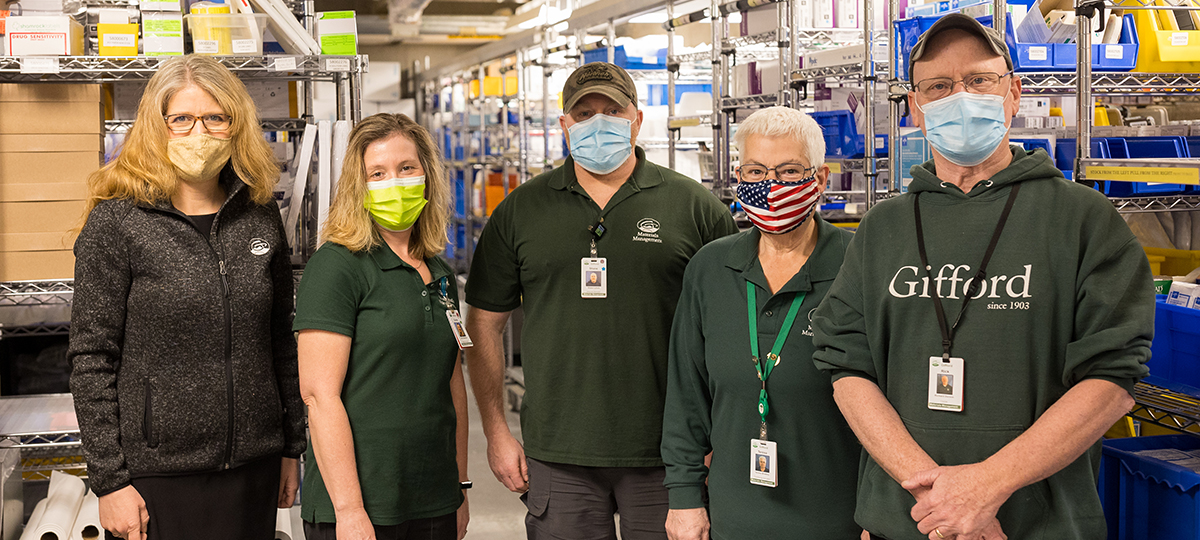
Gifford’s Materials Management Team (from left) Laura Auszura, Carol Wakefield, Shane Lyford, Teresa Bradley, and Rick Dorson
“Laura and the Materials Management team saw that we never had a problem with PPE. They did a great job.”
– Dr. Joshua White
Chief Medical Officer
“Laura never wavered under the stress of shortages and substitutions. She was always willing to chase any opportunity to provide whatever was needed to support patient care and COVID activities, and always with a smile and word of encouragement.”
– Karin Morrow, RN
Director of Nursing
In this Q&A with Laura Auszura we talk about the Materials Management team, what they do to keep the hospital and clinics humming, and strategic planning during the COVID-19 pandemic.
G: Please describe your role at Gifford and who works with you in Materials Management.
LA: I’m the materials manager. I manage purchasing, shipping and receiving, and the mail room, and work with a wonderful team. Teresa Bradley is our purchasing specialist; she deals directly with vendors and places orders. Carol Wakefield is a materials specialist; she primarily manages supplies and fills orders for our clinics and hospital. Each department has a storage area and supplies that staff use on a regular basis, and there are supply exchange carts in the Emergency Department, Operating Room, Birthing Center, and Howell Pavilion. Staff members expect what they need to be there, and Carol works to ensure that it is by checking the carts and restocking as necessary. Shane Lyford is also a materials specialist; he is in charge of shipping and receiving, verifying orders, and staging them for distribution. Last but not least, our courier, Rick Dorson, is responsible for all incoming and outgoing mail. Every day he distributes mail and delivers supplies to offsite clinics.
G: Why do you choose to work at Gifford?
LA: The position attracted me. It’s work that I was very interested in and thought I could excel at doing. I quickly fell in love with the Gifford community and my coworkers. I love being a part of the culture here and contributing every day.
G: Tell us why Materials Management is so important.
LA: Without the essential supplies, whether it be cleaning supplies for Environmental Services or medical supplies for General Surgery, no one can do their job. Materials Management is really integral to the organization. We manage costs, purchase on contract, and manage vendor relationships.
G: How has your work changed or intensified with COVID-19 and the pandemic?
LA: In normal, pre-COVID times, we typically bring in supplies as we need them due to storage limitations. We generally maintain a two-week supply but are constantly replenishing. The pandemic really changed that due to supply shortages. Now, we bring in a three- to six-month supply to make sure we have what we need to sustain us. We’ve had to find overflow storage, and clearly define what is essential to have on hand. That is mainly personal protective equipment (PPE).
When I first started hearing about the pandemic, I anticipated increased need for PPE and started ordering extra to make sure we had supply on hand. Very soon after, our distributors started putting everyone on allocation and limiting how much we could purchase in any given month. So, it has been a year of purchasing what I can, in the quantities that I can, and always trying to stay one step ahead and anticipating what may be the next shortage.
To date we have not run out of anything. We have been able to maintain supplies by staying informed, acting quickly when new information is released, and listening to our vendors.
G: Tell us about your role on Incident Command.
LA: I am on Incident Command to bring updates about our supplies and inform leadership of any areas of concern that we may need to address. Without the necessary supplies we can’t function as a hospital. I take back an understanding that helps drive my purchasing decisions.
G: How have you met any specific challenges you have faced in terms of keeping Gifford supplied over the course of the pandemic?
LA: We’ve been able to meet any challenges we’ve had by working collaboratively with Incident Command. For example, we made changes to the way staff uses PPE, extending its use and reuse. We also moved to washable isolation gowns instead of disposable. We’ve been thinking outside of the box and doing things that are nontraditional. We’ve also been fortunate to have the support of our greater community. They have made tons of donations, to include cleaning supplies and hundreds of handmade masks.
Currently the biggest challenge that I am working to address is needles and syringes. Supply worldwide is strained, given vaccines. It’s the biggest challenge I have faced since the pandemic started.
G: Have you made any pandemic-related changes that you think you’ll adopt permanently?
LA: One thing we did was start purchasing reusable N95 masks that have replaceable filters. Staff love them. The masks are very comfortable, and offer extended use and wear. We have rolled out the masks to about 100 staff members so far. This is something we will continue to do going forward. Also, the masks are made in New Hampshire, so it’s great to support a New England company.
G: How are you and your team doing?
LA: The Materials Management team throughout has been exceptionally committed. They are rock stars and make my job easy. They are great at what they do and very supportive. They have never wavered in their commitment to their jobs, not even in the beginning when there was some fear of working in a hospital. They show up every day and do what is expected of them.
Now, with the vaccine, we have the feeling that the end is close. We look forward to getting back to whatever is the new normal.
G: Anything else you want to share about Materials Management?
LA: We are a department that many people may not even know exists. This pandemic, for us, really highlighted how important our roles are. It makes us proud of what we do and why we come back every day. Even though we don’t have direct patient contact, we know that what we do supports the awesome patient care that Gifford delivers.
G: Thank you, Laura!
###